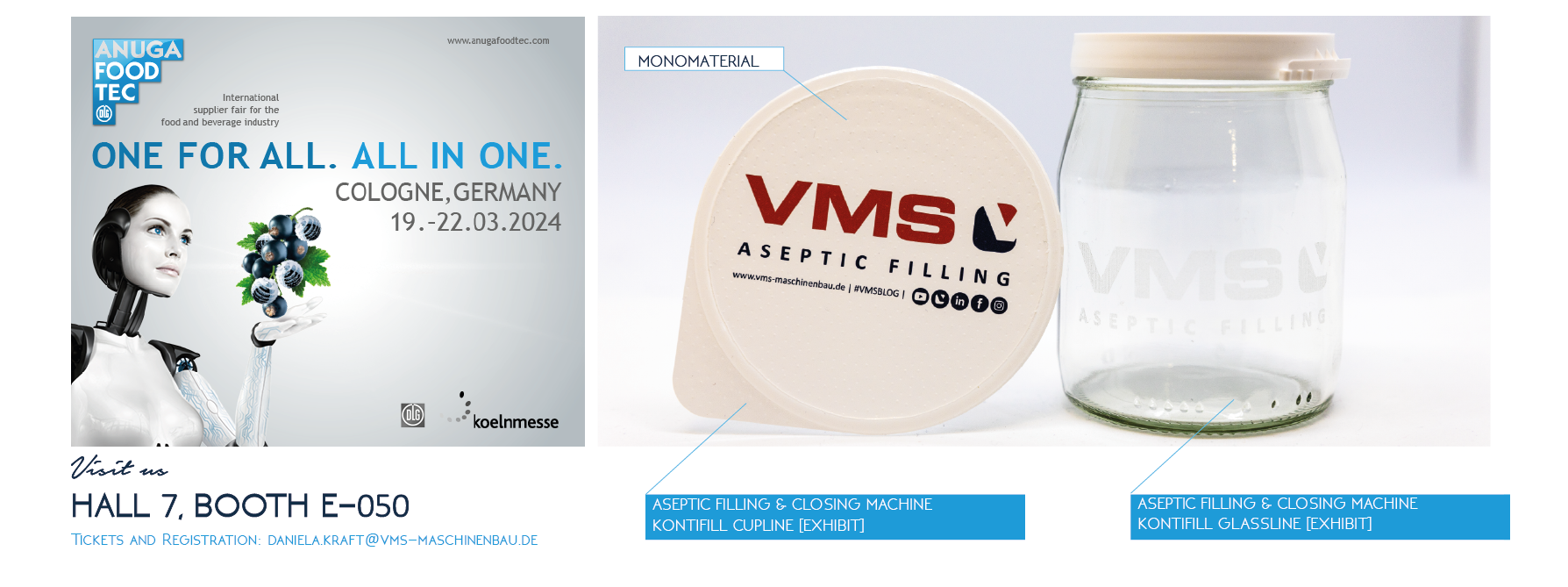

MONOMATERIAL PP & PET
We will present you the oppertunities and possibilities of processing mono materials on our KONTIFILL LINES. We present to you our new sealing process for PP lids as well as our sterilization process which is developed for the requirements of PP and PET materials. At our booth you will find different mono material sealed samples for cups with different lid manufacturers.

THE TRADE EXHIBIT KONTIFLL CUPLINE
The KONTIFILL CUPLINE fair exhibit has seven fillers installed, is flexible in format and has the hygenic class aseptic log6 . Visit us in Colone on our booth and find more details about the VMS technology on the topic of aseptic filling machines for cups, glass, bottles and buckets.
CUPS:
PS / PP/ PET / PP-Paper composite/ Paper
LID:
Alu / PET-Alu / Multilayer / PET / PP / Paper composite
SERVICES FROM - TO:
8.000 cups/ h – 38.000 cups/ h
HYGIENE STANDARD FROM- TO:
Ultra Clean (VDMA IV) and Aseptik (VDMA V)
CUPLine
The VMS CUPLine model provides our customers with the highest level of hygiene standards up to log6 level. Our seal-less piston fillers guarantee high filling accuracies for many years. Filling systems are Cleaning-in-Place (CIP) and Sterilizing-in-Place (SIP). The CUPline is a continuous motion, high performance (even with low viscosity products) fully servo driven filling system. In terms of product safety and hygiene the unit is fully enclosed in a "tunnel" where sterile air is fed selectively and air exchange between the outside environment and the enclosed sterile tunnel or room is significantly minimized and nearly eliminated.
As a result, the MAC-values are not only met, but even exceeded. The cantilevered servo drives are fully enclosed and isolated in the sterile area. They are easily accessible and serviceable. The space saving system control components are fully integrated reducing start-up times. All product contact areas are sterilized with saturated steam at 143°C. The sterile tunnel is cleaned with hydrogen peroxide. Further disinfection of packaging is also carried out with H2O2. The residual peroxide remaining after the disinfection process is less than 0.5 ppm while maintaining log6 levels. The innovative VMS control package can also be monitored and operated remotely through a standard smart phone or tablet.
Hygiene classes Ultra Clean and Aseptic.
- Kontifill Aseptic corresponds to the VDMA hygiene
classes IV resp. V, depending on VMS aseptic module.
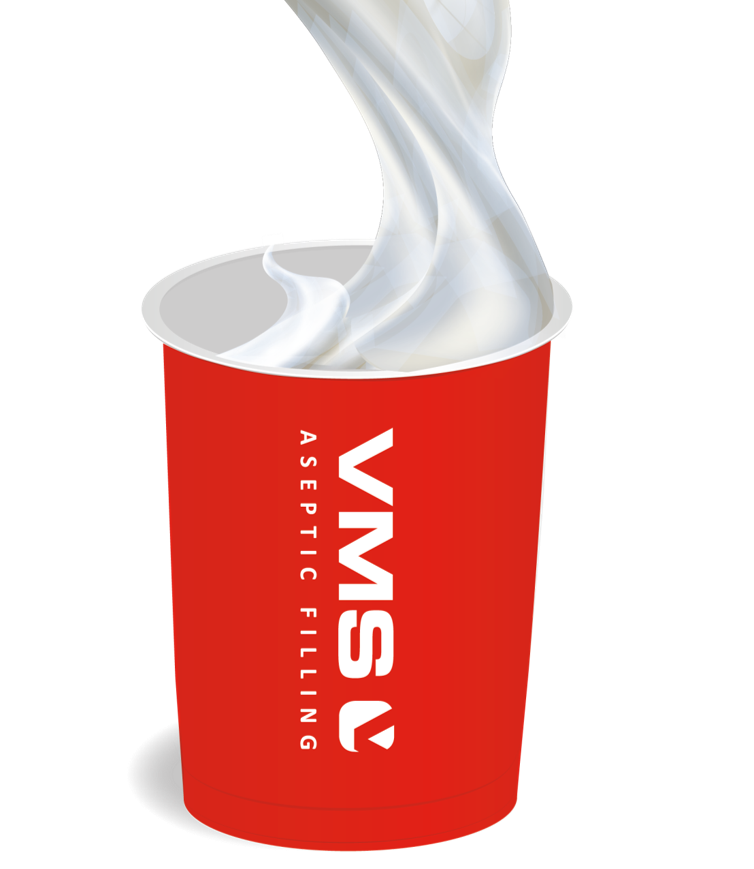

THE TRADE EXHIBIT KONTIFILL GLASSLINE
The KONTIFILL GLASSLINE trade exhibit is a continuously running machine. With the focus on gentle glass handling. Sterilization and filling technology have been developed for gentle and aseptic filling. The KONTIFILL GLASSLINE has an output of 10.000 glasses per hour and can be adapted for different types of lids.
GLASSES:
one-way glass / reusable glass
LID:
tinplate lid:
Twist-Off (TO), Push-On-Twist-Off (PT)
plastic:
PP-Push-On
sealing:
aluminium lid, multilayer lid
SERVICES FROM...TO:
4.000 glasses / h – 20.000 glasses/ h
HYGIENE STANDARD FROM - TO:
ultra clean (VDMA IV) and aseptik (VDMA V)
GLASSLine
Our GLASSLine achieves the highest level of hygiene standards, easily up to log6 level. The sealless piston fillers provide consistently high filling accuracies for serveral years. The machines are designed in Cleaning-In-Place (CIP) and Sterilising-In-Place (SIP). The GLASSline in a genlte continuous motion via servo drives, which ensure high performance and filling reliability even with low-viscosity products.
Due to the completely closed tunnel principle, the sterile air is directed in a targeted manner, so that practically no air exchange takes place between the environment and the sterile room. As a result, the required MAK values are not only adhered to, but even undercut. The sterile area is completely separated from the drive elements. This guarantees quick and easy maintenance access.
All components wich are in contact with the product are sterilized with saturated steam at 143°C. The sterile tunnel is disinfected by hydrogen peroxide. For the sterilization of the packaging material we also use hydrogen peroxide. Because of the special construction, the residual peroxide content is below 0.5 ppm and the germ reduction of log6 is ensured simultaneously.
Our new operating concept enables simple and self-explanatory machine operations even via smartphone and tablet.
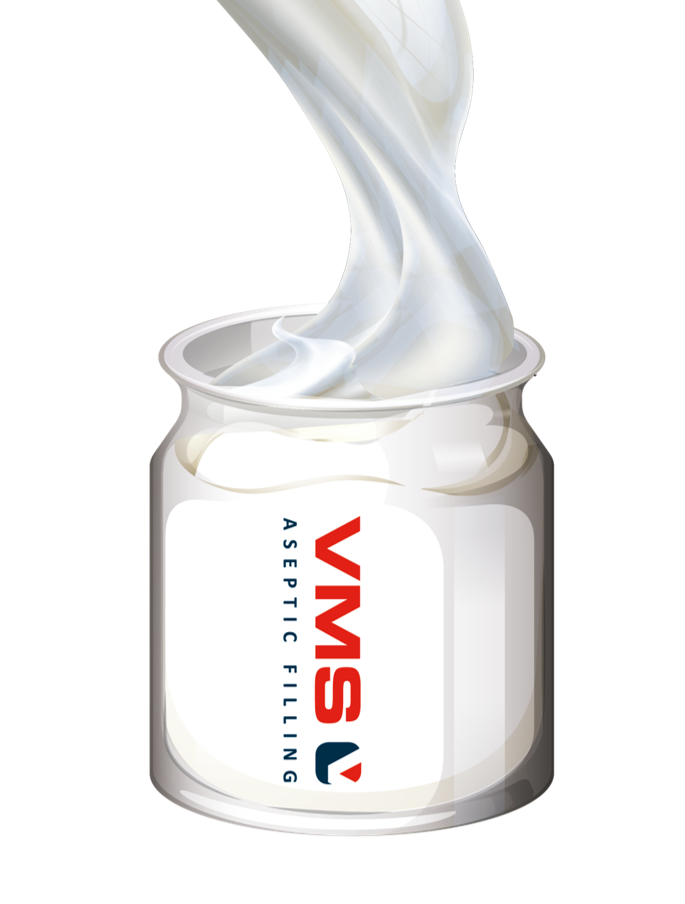

TICKETS & MEETINGS
We would like to invite you to Anuga FoodTec 2024 in Cologne. You can get your ticket at:
This email address is being protected from spambots. You need JavaScript enabled to view it.
Our sales team will be happy to take time for you personally. Arrange an appointment in advance at the VMS booth and let us convince you of the future of aseptic filling and sealing machines!
Your contact:
Daniela Kraft (Head of Sales and Marketing)
This email address is being protected from spambots. You need JavaScript enabled to view it.